How to save a lot of energy with the right hall heating system
January 5, 2023
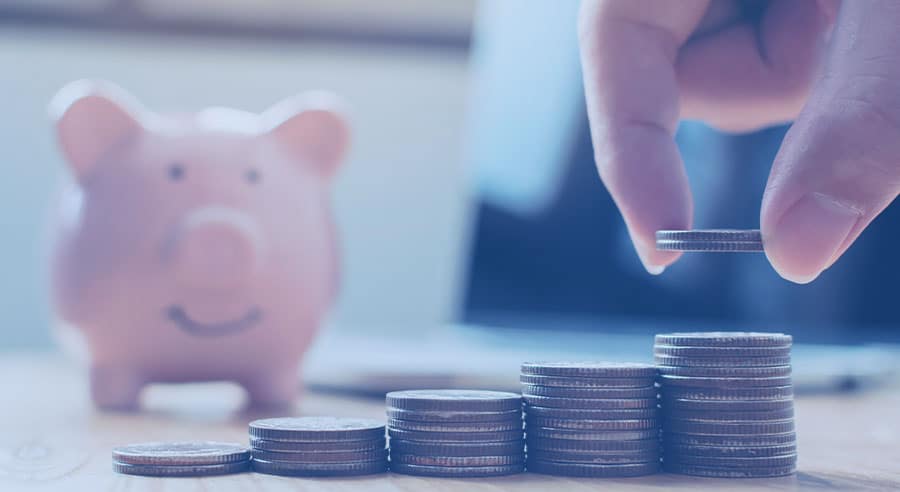
The price of fossil fuels is rising. Also due to the increased CO2-tax. It is becoming increasingly important for hall operators to generate heat in an energy-efficient manner. Find out how the right hall heating system can help you to absorb rising costs.
The energy transition is a challenging time for companies. The country should be climate-neutral by 2045. In future, companies will have to generate electricity and heat exclusively from renewable energies. Unthinkable at the moment. According to the Federal Ministry for Economic Affairs and Energy, the combustion of fossil fuels such as gas and oil covers over 80 percent of heating requirements. In order to accelerate the transformation, the German government is increasing the pressure.
The CO2-Duties on fossil fuels such as heating oil, natural gas and the like are gradually increasing from 45 euros per ton of CO2 in 2024 to up to 65 euros in 2026. From 2027, Europe-wide trading in CO2-emission certificates to the heating sector as well. The CO2-levy is then no longer set at a specific price, but is formed freely on the European market. The CO2-price and therefore the cost of heating oil and natural gas is expected to rise continuously as the number of emission allowances available each year is gradually reduced. Most energy companies will pass these costs on to customers. It can therefore be assumed that heating will become increasingly expensive - heating large areas in industrial halls in particular threatens to become a cost trap. It is therefore important to use energy sources more sparingly and to cushion the rising costs with the right hall heating. How can this be achieved in compliance with the GEG? With modern infrared heating systems, for example.
In order to understand why infrared heaters are the best way to save money, we first need to take a look at conventional heaters. Although they may differ from one another technologically, they generally have one thing in common: they heat air. And hot air rises. In halls with high ceilings, it usually collects at heights where nobody needs it. Operators therefore have to use an unnecessary amount of energy to heat a comparatively small usable area of around two meters above the hall floor - and often use energy-hungry air distribution systems to direct warm air flows downwards. A waste of money par excellence.
Save up to 70 percent on energy costs with infrared heaters
And infrared heaters? They do not heat the air per se. Instead, the devices generate electromagnetic waves that are converted into heat as soon as they hit solid objects - such as the floor, people and machines. This allows the area of use to be heated in a targeted manner, while gigantic air masses above remain unaffected. The devices also react much faster than conventional hall heating because heat does not take the detour via relatively inert water and the air.
When the operator switches the infrared heater on, the heat is available almost immediately. Switching it off is just as quick. If intelligent control systems are added to the mix, the heaters adapt perfectly to the changing heat requirements of everyday life. Without wasting energy. In addition, the auxiliary energy costs are low because the decentralized devices for hall heating only require electricity for ignition, control and the removal of exhaust gases - no energy is required for heat distribution!
The energy savings are impressive: they can amount to up to 70 percent. A saving that compensates for rising fossil fuel prices for years. In addition, employee satisfaction increases. Why? They find the heat particularly pleasant because it corresponds to the natural heating principle of the sun - goodbye dry heating air, swirling dust and draughts. This reduces sickness-related absences and increases productivity.
Point, set and match - how a tennis club reduces heating costs and saves 35,000 liters of heating oil per year
Grün-Weiss Mannheim is one of the largest tennis clubs in Baden. The traditional club operates two halls with ceiling heights of 6.8 meters and a total area of 1,400 square meters. In the past, the club used oil to heat the halls in order to provide the tennis players with sufficient warmth. And consumed up to 35,000 liters per year. Money that the club would rather invest in important things such as youth work.
Those responsible therefore decided to replace the oil heating system. They installed infrared heaters instead. The pitch and the players can now be supplied with targeted heat. The heating temperatures and switching times are controlled via an LCD display in the hall vestibule - individually for each court.
The club saves even more energy by using the waste heat from the heating systems with condensing boiler technology to heat water. Overall, the energy-saving hall heating, intelligent control and residual heat utilization result in savings of 47 percent. Money that now benefits youth work. Point, set and match for Grün-Weiss Mannheim.
Machine manufacturer cuts heating costs from 71,600 euros to 25,000 euros
Textile machinery manufacturer Reiners + Fürst from Mönchengladbach was also faced with the challenge of reducing heating costs. The old heating system: two oil-fired systems with an output of 465 kW each, which had been heating all the buildings via air heaters since the 1980s - the five production and storage halls with an area of 6,300 square meters as well as the 1,200 square meter administration building. The heating system was thirsty and consumed 103,000 liters of heating oil per year. In the winter months, up to 1,000 liters of oil a day. A situation that was no longer acceptable in times of rising prices for fossil-based hall heating.
And so Reiners + Fürst decided to throw out the old oil heating system. The alternative: the H.Y.B.R.I.D. infrared heating system from KÜBLER. The high-efficiency infrared heaters, supplemented by standard appliances, have been doing the heating job ever since. And here too, the infrared heaters only heat the areas where the heat is needed, according to the hall's usage profile.
An intelligent control system adapts the system to everyday life. It independently determines the optimum switch-on and switch-off times and operates the heating at maximum efficiency - depending on shift operation as well as weekend and vacation times. As with the Grün Weiss Mannheim tennis club, the waste heat from the infrared heaters is not lost. The only difference is that the club has gone one step further and combined the energy flows in the halls in a hybrid system. Not only is the waste heat from the heating appliances used, but also that from the hardening furnaces and compressors, for example. Thanks to the O.P.U.S. X heat recovery system, it covers the heating requirements of the 1,200 m2 office space.
Saying goodbye to the old oil heating system quickly paid off for Reiners + Fürst. During the planning phase, the company actually expected to reduce its energy costs by 40 percent. In the end, the bottom line was 65 percent. Heating costs fell from 71,500 to 25,000 euros.
Everything you need to know about energy-saving hall heating systems in practice
Saving energy is a big issue - across all sectors. If you want to put an end to inefficient heating systems, our guide is just right for you!
Request a free guide
You might also be interested in
-
"Heating with the windows open" in private households is like "heating with the doors open" in production halls and warehouses. It's great if you can afford this in industry and commerce because production and business are obviously running - unfortunately, this is not a matter of course for many companies in times of coronavirus.
-
The energy crisis is currently leaving no one indifferent. Everyone is desperately looking for ways to get consumption and costs under control to some extent. The German government's price brake will not take effect until March 2023, and even then, the prices for 30 percent above the basic quota for industry and 20 percent for small and medium-sized enterprises will still be subject to the wild market conditions next year. So what to do?
-
High sickness rates are a burden for many companies. Many companies have discovered that this is not only dependent on the time of year and the incidence of infection, but can also be directly influenced. They are actively working to improve employee satisfaction and are developing suitable programs to increase this important factor.
-
How is energy used correctly? What does efficiency mean? In the German government's current energy policy, there is a huge gap between aspiration and reality. After all, industrial buildings are not treated as industrial buildings because they only account for two percent of buildings - even though they are responsible for 15 percent of greenhouse gas emissions. The latter has not played a role to date. Behind this two percent are 420,000 to 480,000 hall buildings that are used in industry, commerce and municipalities as production halls, logistics halls, workshops, sports halls or sales outlets. A small number that is responsible for a significant proportion of energy consumption and GHG emissions in Germany.